Keeping operating costs under control never has been harder – and more crucial – for manufacturers than now. Automating quality assurance is an effective approach to achieve this. Especially, if you are having a hard time finding skilled labor to run your industrial production processes smoothly. So, what are the options?
Skilled Labor Shortage: A Profit Margin Killer
Planning reliability is easier said than done in 2023. It’s no secret that skilled labor is a bottleneck in manufacturing these days. And this is not likely going to change. Why?
→ Changing markets make it more and more important to venture into new business fields.
→ To ensure more independence and future stability, you probably also have to localize your supply chain.
No matter if you need to localize supply chains, enter new business areas, or both – you’ll need skilled labor for that, and it won’t be cheap. There is not enough skilled labor in the job market and even if you have enough employees to cover all production steps, they probably have to get extensive additional training.
At the same time, the pressure to maintain or improve profit margins is rising. After all, we’re living in times of inflation and slow growth. If quality assurance is a big cost driver for your production (processes), you’ll need to find a way to lower your QA expenses.
Of course, quality assurance and plant managers could lower the standards. But this comes at a high cost. From legal expenses to call-back costs for faulty products, low quality is expensive. Not to mention the reputational damage you will face. If you want to maintain your product and process quality standards while improving your profit margin, you’d want to automate your QA as much as possible.
Automating Quality Assurance
Now, quality assurance can be many things. In this article, we’re talking about:
Ensuring smooth processes: Making sure your company achieves production targets, lowering downtimes, and setting up corrective and predictive actions (CAPAs).
Ensuring product quality: Identifying out-of-specification (OOS) errors and preventing their reoccurrence.
Both aspects go hand in hand. If you identify an OOS error automatedly (e.g. your product surface is not even enough), you can also implement automated CAPAs (e.g. if this error is reported the third time in a row, an email goes out to trigger the replacement of the outworn abrasive paper). From the collected data, you can calculate more precisely, when to re-order production materials (e.g. abrasive paper), making your production plant more efficient. We could spin this further, but you get the picture.
You can automate almost any step in your quality assurance. However, some automated solutions will have a better return on invest (ROI) than others. It really depends on your quality issues. This makes it crucial to get a good overview of the possibilities, before thinking about their potential implementation.
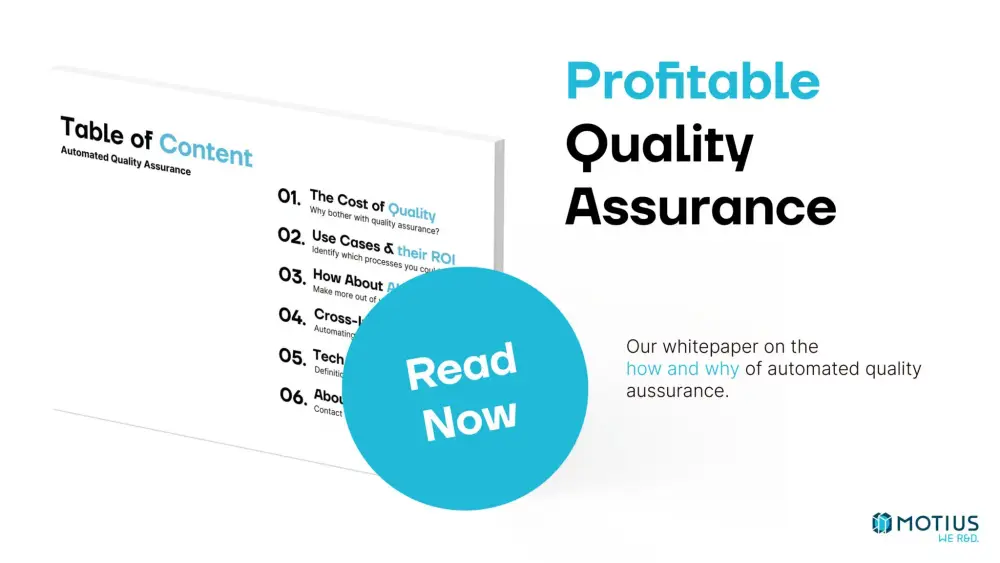
Use Cases for Quality Assurance Automation
Let’s talk about what automating your quality assurance can and can’t do. It can reduce out-of-specification errors, increase efficiency, and improve product quality. It also can provide seamless documentation and ensure quick and reliable corrective actions. Provided that you have repetitive tasks, high production volume and/or high costs for deficient quality (e.g. high call-back costs).
What automated quality assurance can’t do: measure many dimensions at the same time cheaply. The more dimensions, the pricier your sensor and its maintenance will be. The good thing is, that in our experience you often don’t need that many dimensions at once.
Depending on the complexity of your sensors, you can e.g. measure filling levels, check temperatures, recognize false objects, classify objects or even specify chemical compositions. To make this more tangible, here is a fictional manufacturing step, involving a screw:
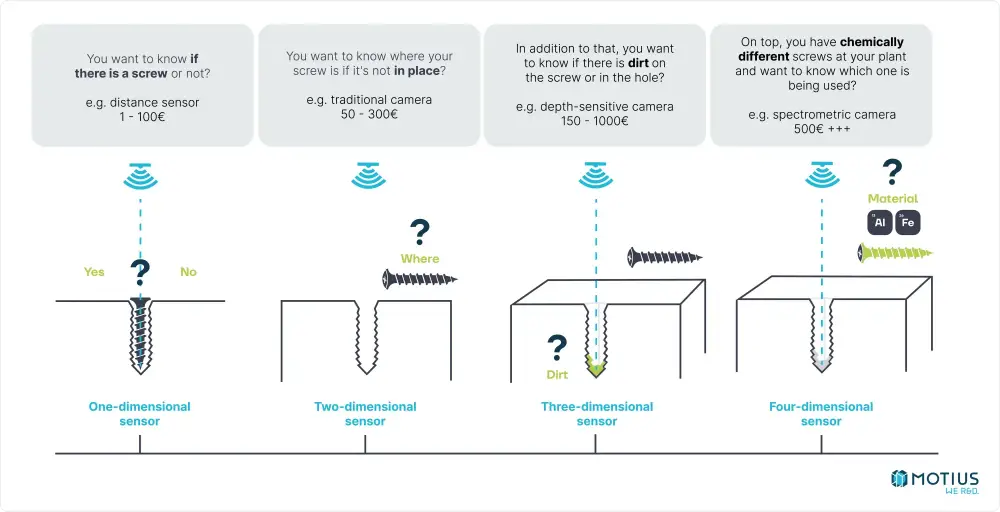
In our Automated Quality Assurance Whitepaper (currently only availabe in German) you’ll get a more detailed overview, of the most frequent aspects you can monitor automatically with sensors. Spoiler: More sophisticated sensors don’t necessarily result in a better ROI. The go-to solution always depends on the requirements and the problem statement.
The ROI of Automated Quality Assurance
Now, the question is: Which approach is feasible and has the biggest effects on your costs? Growth will be slow in 2023, so innovation investments are under high scrutiny. On top, you need to keep an eye out for AI, which is changing the industry rapidly. Automated QA enables you to collect data and with AI you can leverage this data to make ai-based decisions. AI-based tech, like computer vision, is used more and more frequently in automated quality assurance processes.
Want to dig deeper? Download our Whitepaper on Automated Quality Assurance (currently only availabe in German), to learn about:
- break down ROI of different use cases
- explain how to add AI to the mix
- take a deep dive into Computer Vision (one example of using AI in quality assurance)
- give you some real-life examples of projects with MTU and TetraPak
Download it here to assess if QA automation is suitable to reduce your operation costs and grow your business despite skilled labor shortages.
Leverage the Power of Automated Quality Assurance
Over the years, we’ve helped many market leaders to stay on top of their game by implementingindustry 4.0 technologies. In our experience, automated QA is a very reliable tool to tackle the ongoing shortage of skilled labor. But, where and how you automate your quality assurance (processes) best, depends on your use case. Besides knowing your technical options, you also need to really understand your problem statement before you start to automate your QA.